파운드리 공정 엔지니어 업무 실전 편 ②CVD 유형
저는 늘 사용하던 말 들이라 아무렇지 않게 썼는데 반도체를 아예 모르시는 분들이 훨씬 많으니 용어 들에 대해서 설명드리도록 하겠습니다. CVD 유형에 대해서 말씀드려 보겠습니다. CVD 란 Chemical Vapor Deposition의 약자로 한국말로 하면 화학 기상 증착 법을 말합니다. 위키피디아에서만 보더라도 Pressure (압력) , Energy 등 여러 가지로 구별을 하는데 크게 보면 SA (Semi Atmospheric)에서 열 에너지로 Deposition을 하는 방식 / PE (Plasma Enhanced)에서 Plasma를 이용해 Deposition을 하는 방식이 있고 HDP (High Density Plasma) / ALD (Atomic Layer Deposition) / SOG (Spin On Glass) 등의 방식이 있습니다.
1. SA (Semi Atmospheric) CVD
해당 방식은 말 그대로 상압에서 진행하는 공정을 말합니다. 상압에서는 Plasma 생성이 안되기 때문에 주로 열 에너지를 이용하여 Deposition 을Deposition을 하게 됩니다. 주로 SiO2 막질 Deposition을 진행하며 최소 400°C 이상의 공정입니다. 주로 TEOS (Tetraethyl orthosilicate) 같은 Chemical 을 기화시키고 O3 등과 반응을 시켜서 SiO2 막질을 증착시키는 방식입니다. Step Coverage (Pattern을 따라서 잘 deposition이 되는지 여부)가 좋은 편이라 Gap-fill이나 Spacer 등의 용도로 많이 사용이 됩니다.
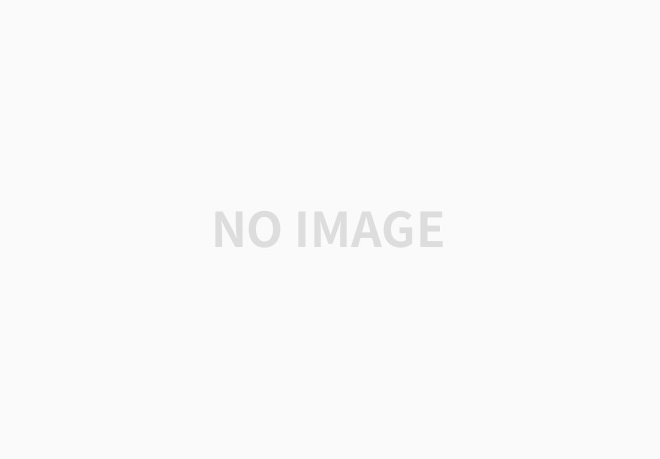
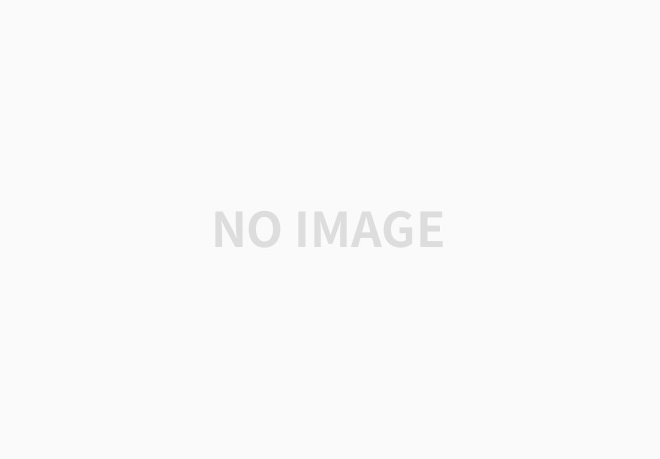
2. PE (Plasma Enhanced) CVD
PE 는 Deposition 이 이뤄지는 Chamber 내부를 진공에 가깝게 유지한 상태에서 Plasma를 이용해서 Deposition을 하는 방식을 말합니다. 반응을 시킬 Gas를 Chamber 안으로 flow 시키고 RF를 인가해서 Plasma를 만들고 이러한 Plasma를 이용하여서 Deposition을 하는 방식입니다. Plasma를 사용하기 때문에 SA 방식에 비해 상대적으로 저온에서도 증착이 가능한 편이고 Deposition 속도도 빠른 편입니다. RF를 사용하는 만큼 Power 생성을 위한 Generator , 설비에서 Reflect 등을 조절하기 위한 Matcher 등의 Parts가 추가로 필요하며 관리 요소가 많아지는 만큼 조금의 변동으로도 막질의 물성이 변할 수도 있습니다.
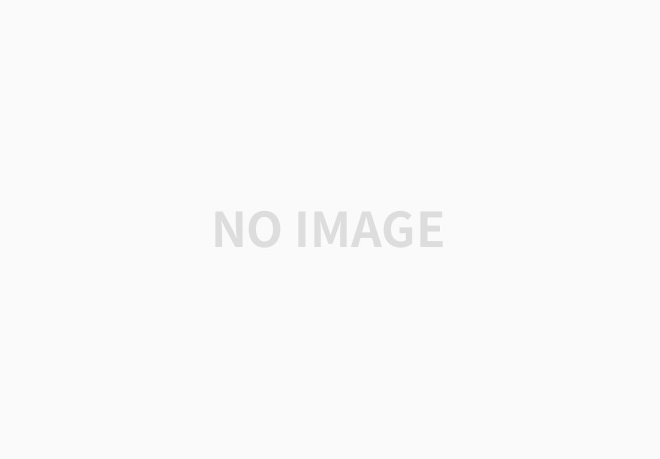
3. HDP (High Density Plasma) CVD
기본적으로는 PE CVD 방식과 동일합니다. 즉 Plasma 를 이용하여서 Deposition을 하는 방식입니다. 하지만 초진공 상태를 만들어서 (PE CVD의 경우 Pump 1개 사용 , HDP는 Turbo Pump 추가로 장착) 조금 더 고밀도의 Plasma를 만들고 이를 이용하여서 Depo와 Etch를 동시에 하는 효과를 낼 수 있는 공정입니다. 고밀도의 Plasma를 사용함으로써 훨씬 dense 한 막질을 만들 수 있고 RF Power 인가할 시 Deposition Gas 가 아닌 비활성 Gas (Ar 등)만 flow 한다면 Wafer 표면을 때려서 Etch 하는 효과를 만들기도 합니다. Gap-fill을 할 경우 Depo 후에 Etch를 통해 개구부를 넓히고 다시 Depo를 하는 방식으로 Void 없게 진행이 가능합니다.
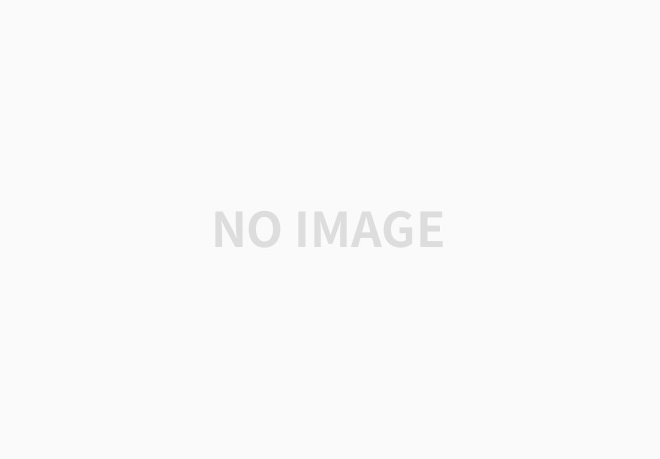
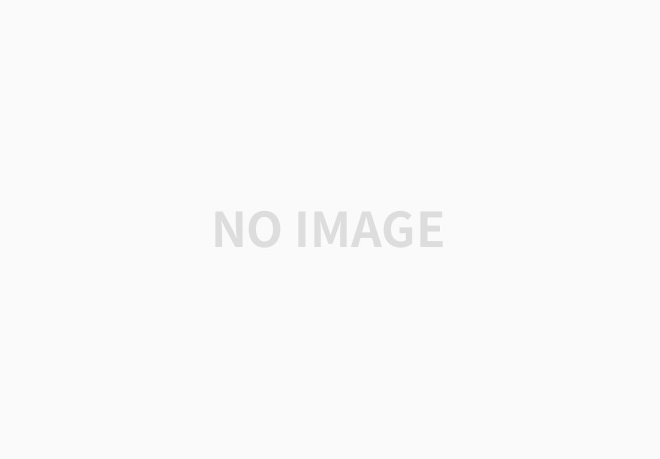
4. ALD (Atomic Layer Deposition)
상대적으로 최근에 개발된 공정입니다. 아래 그림과 같이 Source를 feeding 하고 반응하지 않는 Source는 Purge , 이후에 RF를 인가해서 1개의 Layer 를 만드는 방식을 계속 반복해 나가면서 층을 쌓아 나가는 방식입니다. 매우 낮은 THK에 대해서도 미세한 Control 이 가능하며 저온에서도 진행이 가능하여서 Heat Budget (Metal Gate 등이 생성된 상태에서 고온이 가해질 경우 Gate 성능이 열화 가능성 존재)에 대한 우려가 없습니다. Step Coverage 도 매우 우수한 공정으로 거의 1:1 가량 진행이 가능합니다. FinFet 공정에 꼭 필요한 공정입니다.
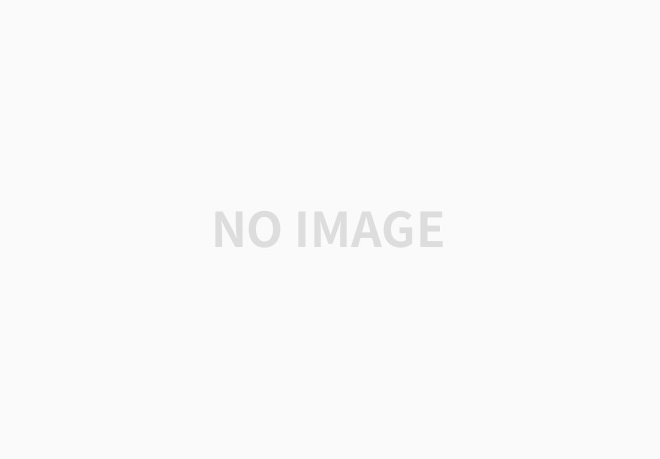
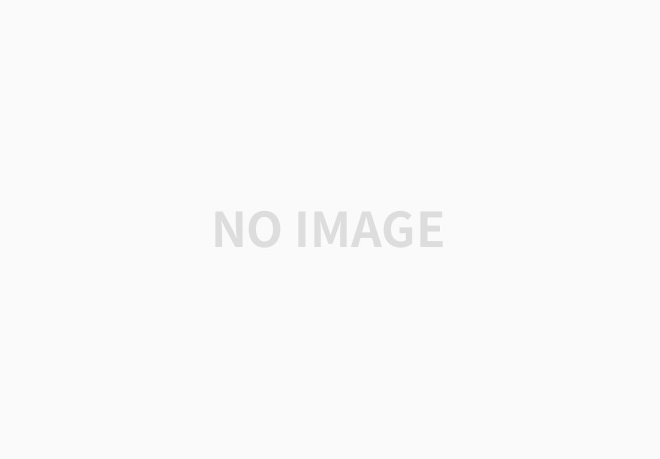
5. SOG (Spin On Glass)
이 방식은 기존 방식과 좀 다르게 Deposition 을 하는 방식입니다. 위에 방식들 모두 Gas 나 Chemical (기화시켜서)을 Wafer 위에서 열이나 Plasma를 이용해서 반응을 시키는 방식인데 반해 SOG는 회전하는 Wafer 위에 액체 상태의 Chemical을 그대로 뿌리고 회전하는 원심력을 이용해서 고르게 퍼트리는 방식입니다. 장점으로는 액체의 특성을 살려서 Aspect Ratio (가로 대 세로의 비)가 높은 영역에서도 손쉽게 Gap-fill 이 가능합니다. 단점으로는 CVD 및 ALD 방식과 달리 THK를 Control 하는데 한계가 있으며 후속에 Anneal 공정을 진행하여서 막질을 dense 하게 만들어줘야 합니다. 즉 필요한 공정 수가 늘어나게 되는 것입니다.
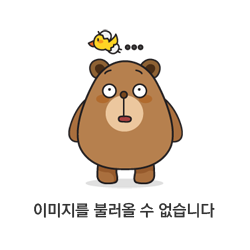
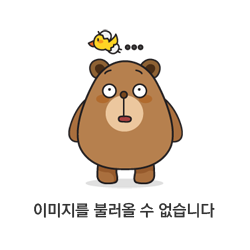
CVD 유형에 대해서 간략히 다뤄 보았습니다. 책에 보면 훨씬 더 다양한 기준으로 나누고 있고 저도 그렇게 배운 채로 회사에 입사했었습니다. 하지만 실제로는 거의 위에 5개 정도로 구별을 하고 있으므로 5가지로 알고 게셔도 크게 문제는 없을 것으로 보입니다.
감사합니다!
'반도체 파운드리 REAL 업무' 카테고리의 다른 글
파운드리 공정 엔지니어 업무 실전 편 ③Interlock 설비 편_2 (12) | 2022.10.21 |
---|---|
파운드리 공정 엔지니어 업무 실전 편 ③Interlock 설비편_1 (14) | 2022.10.14 |
파운드리 공정 엔지니어 업무 실전편 ①NPW BACK UP (27) | 2022.10.11 |
파운드리 공정 엔지니어 업무 (55) | 2022.10.10 |
파운드리 설비 엔지니어 업무 (38) | 2022.10.09 |
댓글